Your Total Manual to Preventing Weld Undercut Like a Pro
Your Total Manual to Preventing Weld Undercut Like a Pro
Blog Article
Mastering the Art of Welding: How to Avoid Undercut Welding Issues for Flawless Construction Outcomes
By recognizing the root triggers of undercut welding and applying effective strategies to stop it, welders can boost their craft to brand-new degrees of excellence. In the quest of perfect manufacture outcomes, mastering the art of welding to stay clear of undercut concerns is not just a skill yet a requirement for those aiming for perfection in their work.
Understanding Undercut Welding

To prevent undercut welding, welders ought to make certain correct welding parameters, such as changing the existing, voltage, travel rate, and preserving the appropriate electrode angle. Additionally, making use of the suitable welding strategy for the specific joint configuration is crucial. Utilizing weaving motions or backstepping techniques can assist make sure correct weld metal deposition and lower the likelihood of undercut formation. Routine assessment of welds during and after the welding process is likewise critical to catch any undercut early and make needed changes to prevent additional flaws. Preventing weld undercut. By recognizing the sources of undercut welding and carrying out safety nets, welders can attain top quality, structurally audio welds.
Reasons For Undercut in Welding
Understanding the elements that contribute to damage in welding is crucial for welders to produce top notch, structurally sound welds. Insufficient welding current or inaccurate welding speed can additionally contribute to undercut. Comprehending these reasons and carrying out appropriate welding techniques can assist protect against undercutting problems, making certain long lasting and solid welds.
Techniques to avoid Undercutting

To mitigate the risk of undercutting in welding, welders can utilize tactical welding techniques aimed at boosting the top quality and integrity of the weld joints. Furthermore, using the correct welding technique for the specific joint arrangement, such as weave or stringer grains, can add to reducing damaging.
In addition, appropriate joint preparation, including making certain tidy base materials devoid of contaminants and making use of the proper welding consumables, is crucial in avoiding undercut defects. Using back-step welding methods and controlling the weld grain account can additionally assist distribute warmth uniformly and minimize the threat of undercut. Normal assessment of the weld joint during and after welding, as well as carrying out high quality guarantee actions, can assist in resolving and discovering undercutting issues promptly. By applying these techniques faithfully, welders can accomplish remarkable manufacture results with marginal undercut defects.
Value of Correct Welding Parameters
Choosing and preserving ideal welding parameters is crucial for accomplishing successful welds with very little issues. Welding parameters refer to variables such as voltage, existing, travel speed, electrode angle, and shielding gas flow rate that directly impact the welding process. These specifications need to be meticulously readjusted based upon the kind of material being bonded, its thickness, and the helpful resources welding technique employed.
Appropriate welding specifications ensure the correct amount of warm is used to thaw the base metals and filler material consistently. If the specifications are set too expensive, it can cause extreme heat input, causing distortion, burn-through, or spatter. On the other hand, if the parameters are also reduced, incomplete fusion, lack of infiltration, or damaging might happen.
Quality Control in Welding Procedures
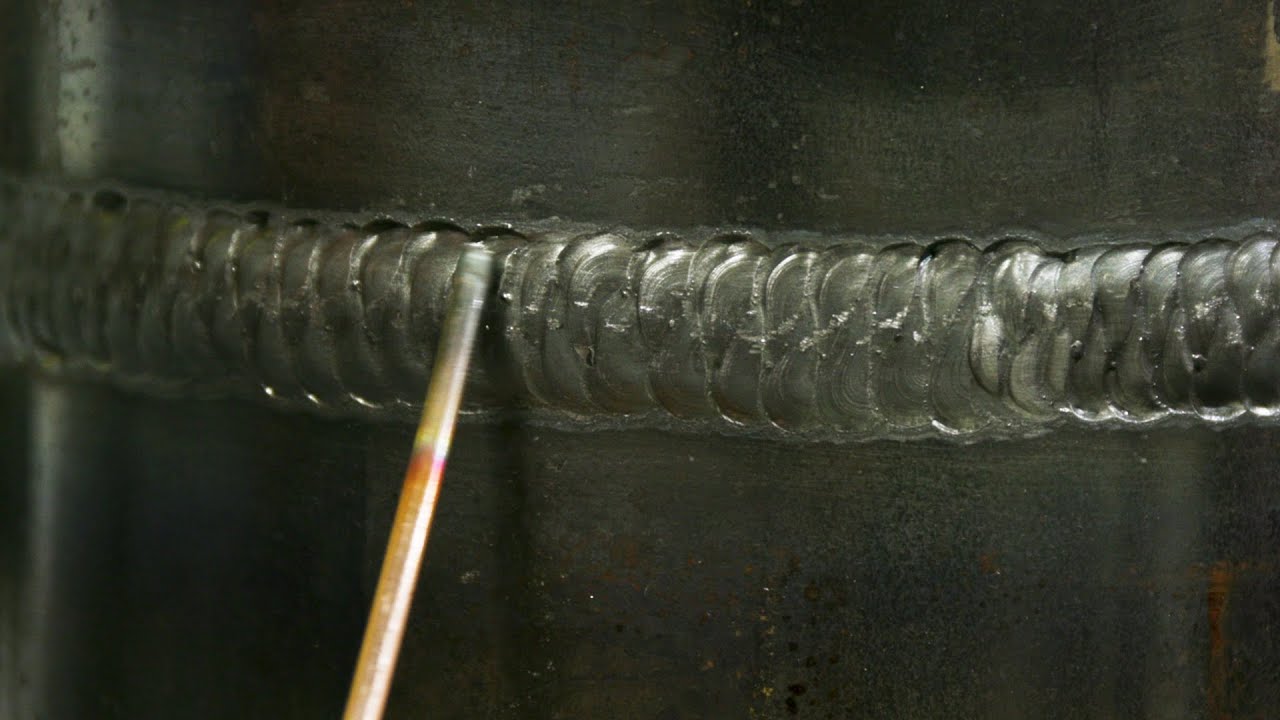
Final Thought
Finally, understanding the art of welding needs a complete understanding of undercut welding, its causes, and methods to avoid it. By ensuring correct welding specifications and implementing top quality assurance practices, flawless manufacture results can be attained. It is vital for welders to regularly make every effort for quality in their welding operations to stay clear of undercut problems and produce top notch welds.
Undercut welding, a common issue in welding procedures, happens when the weld steel doesn't effectively fill the groove and leaves a groove or clinical depression along the welded joint.To prevent undercut welding, welders need to guarantee correct welding parameters, such as changing the existing, voltage, travel rate, and preserving the proper electrode angle. Inadequate welding existing or incorrect welding rate can likewise contribute to undercut.To alleviate the threat of undercutting find more information in welding, welders can utilize critical welding methods aimed at enhancing the high quality and honesty of the weld joints.In verdict, mastering the art of welding needs an extensive understanding of undercut welding, its reasons, and techniques to prevent it.
Report this page